外観検査の自動化に取り組みたい・目視検査を機械やロボットに置き換えたいとお考えですか。
本記事では、外観検査の自動化のメリットや取り組む際の課題や問題点を紹介します。さらに成功事例や進め方、失敗しないコツも紹介します。
ファクトリーオートメーション化のプロが徹底解説するので、工場における外観検査を自動化したいという方は、ぜひ最後までご覧ください。
\ 話を聞いてみたいだけでもOK /
外観検査の自動化とは
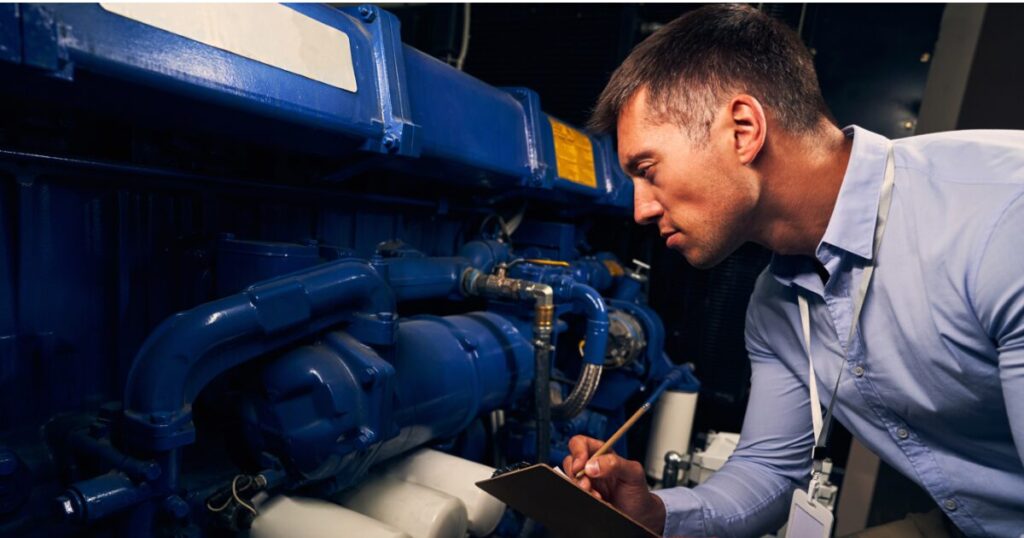
外観検査の自動化とは、製造された部品や製品の表面に発生するキズ、汚れ、異物、変形などの欠陥を、従来の目視検査からカメラやセンサー、AIなどの技術を用いた自動システムによって検出・判定する仕組みです。
もともと外観検査は、製品の品質を保つうえで重要な工程であり、多くの工場では熟練の検査員が自らの目で状態を確認していました。しかし、人による検査は作業者の集中力や経験に左右されやすく、検査品質のバラつきや見落としのリスクが課題でした。
こうした課題を解消する手段として注目されているのが、外観検査の自動化です。高精度カメラや照明装置、画像処理ソフトウェア、さらにはディープラーニングを活用したAIによる判断機能を組み合わせることで、人の感覚に頼らず、安定した検査を実現できます。
現在では、自動車・電子部品・医薬品・食品業界など、ミスの許されない高品質が求められる業種を中心に、自動化ニーズが急速に高まっています。近年のAI技術の進化により、従来のルールベースでは難しかった柔軟な判別も可能となり、さらなる導入の加速が期待されています。
ここでは外観検査の自動化について説明しましたが、工場以外全体の自動化について知りたい方は以下の記事も参考にしてください。
工場の自動化とは?メリット・課題・成功事例・進め方を徹底解説
外観検査(目視検査)を自動化を導入するメリット
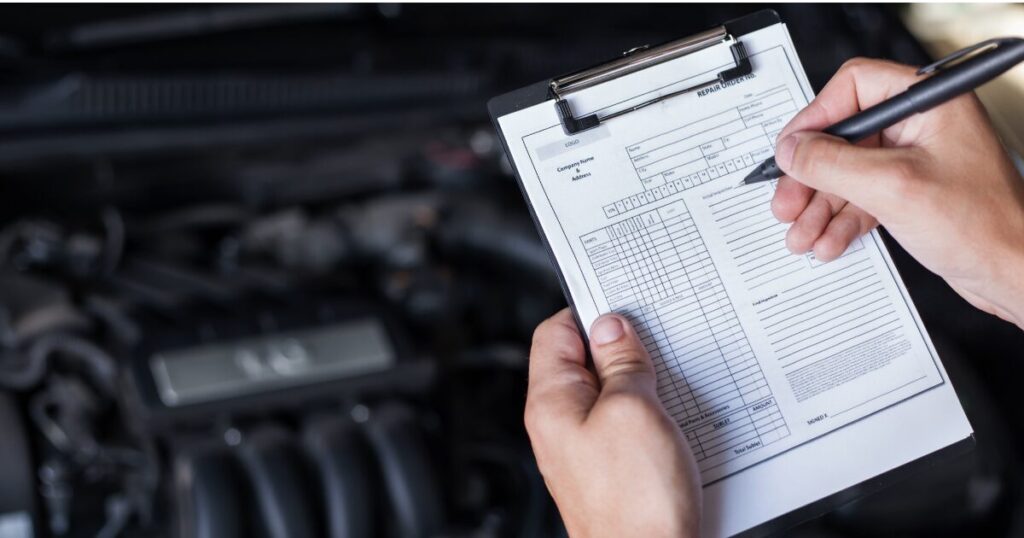
外観検査の自動化には、目視検査では避けられなかった課題を解消する多くの利点があります。ここでは、主なメリットを解説します。
- 外観検査にかかる時間を短縮できる
- 外観検査にかかるコストを削減できる
- ヒューマンエラーの発生を防止できる
- 人手不足・技術継承の問題の将来的なリスクを回避できる
- 工場の外観検査の結果をデータとして蓄積できる
それぞれ見ていきましょう。
外観検査にかかる時間を短縮できる
自動化された外観検査システムは、対象製品を高速かつ連続的に検査できるため、従来の目視検査と比べて処理スピードが大幅に向上します。
人間のように疲労によって集中力が低下することもなく、長時間の稼働が可能です。結果として、検査工程のボトルネックが解消され、生産ライン全体のスループット改善にもつながります。
外観検査にかかるコストを削減できる
導入初期には一定の設備投資が必要ですが、中長期的には人件費や教育コストの削減によって、総合的な検査コストを下げることが可能です。
検査員の採用・育成にかかる負担を軽減できる点は、製造業にとって大きなメリットです。加えて、検査ミスによる不良品流出のリスク低減もコスト削減の一環といえます。
ヒューマンエラーの発生を防止できる
目視検査では、どうしても作業者の体調や熟練度により精度にばらつきが生まれがちです。これに対し、自動化された検査システムは常に一定の条件で検査を実施できるため、ミスの発生を抑えることができます。
また、再検査やクレーム対応にかかる工数も削減され、品質管理体制の強化にもつながります。
人手不足・技術継承の問題の将来的なリスクを回避できる
製造業では少子高齢化の影響で、現場の人材確保や技術の継承がますます困難になっています。特に目視検査は熟練者の経験が求められる工程であり、技術者の高齢化とともに品質維持のリスクが増加します。
自動化を進めることで、属人性の高い作業からの脱却が図れ、将来的な人材不足の影響を最小限に抑えることができます。
工場の外観検査の結果をデータとして蓄積できる
自動化システムは、検査の結果や不良の傾向などをリアルタイムで記録・蓄積することが可能です。これにより、過去の検査履歴をもとにした不良原因の分析や品質改善活動がしやすくなり、製造プロセス全体のPDCAを効率的に回すことができます。
検査結果の可視化や共有も容易になり、品質管理体制の高度化に貢献します。
外観検査を自動化するのは難しい?自動化する上での課題
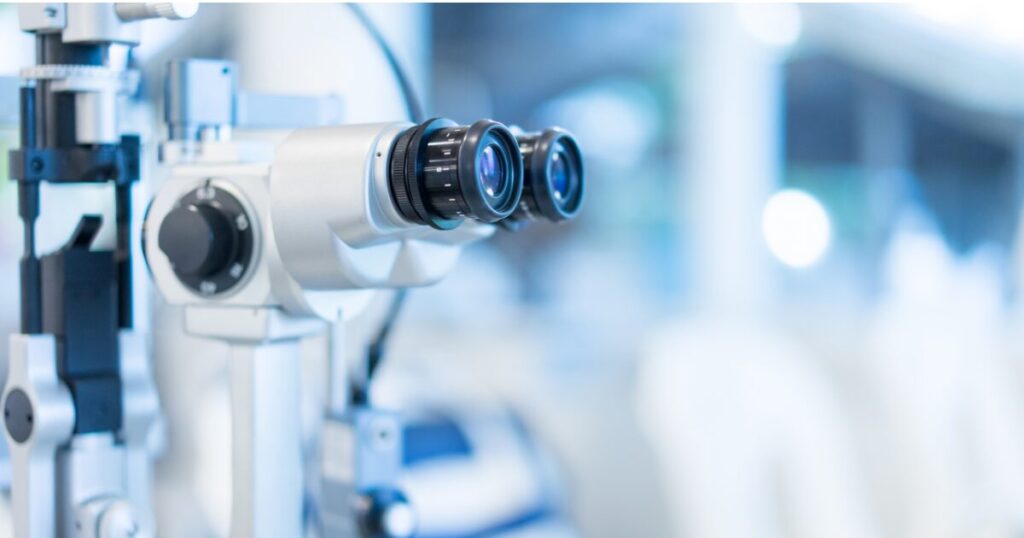
外観検査の自動化は多くのメリットがある一方で、導入にあたっては乗り越えるべき課題も存在します。特に、製造現場の環境や生産体制によっては、自動化が難航するケースもあります。ここでは、自動化導入時に直面しやすい代表的な課題を解説します。
- 工場ごとに機器のカスタマイズが必要である
- ティーチングする人材の確保が必要である
- 多品種・少数生産を行う工場には不向きである
- 臨機応変な対応が難しい
それぞれ見ていきましょう。
工場ごとに機器のカスタマイズが必要である
外観検査用の装置は、一般的に一定の汎用性を持って開発されていますが、実際の製品形状や材質、検査ポイントは工場ごとに異なります。そのため、自社製品に適した検査精度や検査条件を満たすには、装置のカスタマイズや専用治具の設計が必要になる場合が多く、導入までの工数やコストがかかります。
特に高精度な検査が求められる業界では、標準仕様のままでは対応できないケースが珍しくありません。
ティーチングする人材の確保が必要である
自動化機器の導入には、「ティーチング」と呼ばれる設定作業が欠かせません。これは、装置に検査動作や基準を覚えさせるプロセスであり、専任のスキルを持った人材(ティーチングマン)が必要です。
しかし、こうした人材は市場でも不足しており、外注する場合は費用が高騰し、自社で育成する場合は長期的な投資が求められます。導入タイミングや規模によっては、人材不足がボトルネックとなる可能性もあります。
多品種・少数生産を行う工場には不向きである
検査の自動化は、同一製品を大量に生産する場合に特に効果を発揮します。一方で、品種の切り替えが頻繁に発生する多品種少量生産の現場では、製品ごとの設定変更や再ティーチングが必要になるため、効率が下がりがちです。
また、検査対象が都度変わるような現場では、柔軟に対応できる自動検査システムを構築するのが難しく、コストや運用負荷が大きくなりやすいのが実情です。
臨機応変な対応が難しい
人間の目視検査には、その場の状況に応じた柔軟な判断や微調整が可能という強みがあります。これに対し、機械による自動検査はあらかじめ設定された基準に従って動作するため、想定外の不具合や例外ケースに対しては対応が難しい場面もあります。
こうした理由から、多くの工場では完全自動化ではなく、人によるチェックと機械検査のハイブリッド運用を採用しています。機械だけではカバーしきれない領域が存在することを認識しておく必要があります。
外観検査の自動化の成功事例
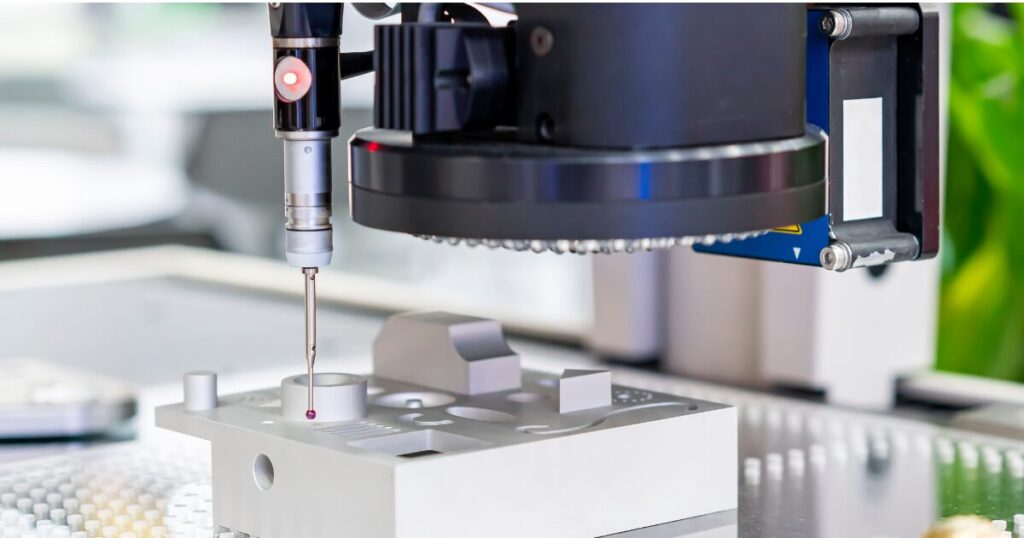
ここでは外観検査の自動化に成功した企業を経済産業省のロボット導入実証事例をもとに紹介します。
- 機能展開型SIプロセスによる薄板板金プレスの自動化
- 協働ロボットと人工知能技術を組み合わせた多品種油圧機器外観検査作業の省コスト化
- 切り替えレス多品種対応自動化ラインによる生産プロセス効率化
- 双腕型ロボットを活用した複数システム兼用可能な自動車部品の検査梱包工程の自動化
ぜひ参考にしてください。
機能展開型SIプロセスによる薄板板金プレスの自動化
精密プレス部品を製造する株式会社北斗は、薄板板金プレス部品の検査・搬送工程にロボットを導入しました。従来の「作業置換型」ではなく「機能展開型」のSI手法を採用することで、導入コストを大幅に削減。労働生産性が16倍に向上し、不良品の流出も抑制されました。
導入前の課題
事務機器部品の多品種少量生産化が進み、従来の生産方式では利益確保が困難になっていました。また、検査工程が目視に頼っていたため、作業者による検査品質にばらつきが生じ、不良品の流出が問題となっていました。
導入されたロボットとSIer
スカラロボット、材料位置決めロボット(ヤマハ発動機、オリイメック YK1200X)が導入されました。システムインテグレーター(SIer)は株式会社エフエーシステムです。
解決策と導入効果
「機能展開型」というSI手法を採用し、ロボット導入費用を大幅に削減しました。加工対象製品をカメラでスキャンして形状を認識させ、加工プログラムを自動で起動する仕組みを構築。さらに、検査工程にはカメラによる画像処理機能を付加したスカラロボットを導入し、良品・不良品の自動判定と分別を可能にしました。
この導入により、人件費や加工費を大幅に削減し、費用対効果の高い設備投資が実現しました。労働生産性は16倍に向上し、不良品の流出が抑制されました。また、熟練技術者を必要とせず、オペレーターは特別な技能なしにシステムを稼働させることが可能となり、多品種少量生産の合理化が進みました。投資回収年数は4.8年です。
協働ロボットと人工知能技術を組み合わせた多品種油圧機器外観検査作業の省コスト化
稲坂油圧機器株式会社は、建機用油圧パイロット弁の最終検査である外観検査に、画像AIとロボット技術を導入し自動化しました。これにより、良品判定の精度が向上し、生産性が大きく向上。人と協働するシステムの構築により、従来のスペースを活用した自動化も実現しました。
導入前の課題
建機用油圧パイロット弁の最終工程における外観検査は熟練検査員を必要とし、自動化が最も遅れている分野の一つでした。検査には「良い眼と集中力」が求められるため、若い人材しか対応できず、人手不足が深刻でした。また、鋳物製品であるため、グラインダ仕上げ跡と不良の傷の区別が難しいという課題や、既存工場スペースの制約も存在しました。過去には画像処理を使ったチャレンジでは良い結果が得られませんでした。
導入されたロボットとSIer
双腕型スカラロボット「川崎重工業 WD002N/duAro」安達株式会社です。
解決策と導入効果
AI技術とロボットを組み合わせて外観検査を自動化しました。上面は固定カメラで、側面と底面は双腕ロボットの両腕に配置したカメラで撮影し、取得した画像をAI技術で良品画像と比較して自動で良品・不良品を判断します。AIの学習には良品画像を提供するだけで対応可能です。安全柵が不要な協働ロボットの採用により、既存スペースでの導入が可能となりました。
この結果、労働生産性は10倍に向上し、作業者による検査品質のバラつきがなくなり、品質の安定が実現しました。製品の更改にも容易に対応できる柔軟性を持ち、投資回収年数は4.6年です。
切り替えレス多品種対応自動化ラインによる生産プロセス効率化
紀伊産業株式会社は、メイクアップ化粧品の仕上げ包装工程にラベル貼りや小物装填を行うロボットを導入しました。機械的な規制機構を排除し、複数形状の製品に柔軟に対応できるロボットシステムを構築。これにより、従来の課題であった多品種少量生産における高額なシステムインテグレーション費用を大幅に削減しました。
導入前の課題
メイクアップ化粧品の仕上げ・包装工程は、頻繁なデザイン変更のためほとんどが人手に頼っていました。品質要求の厳格化に伴い、検査機器の導入や要員の追加により生産コストが増加し、作業ミス防止策として生産スピードが低下していました。
さらに、少子高齢化による慢性的な人材不足が重なり、労働生産性が著しく低下していました。従来の自動化手法では、製品ごとにガイドや冶具の設計が必要で、システムインテグレーション費用が高額になることも課題でした。
導入されたロボットとSIer
パラレルリンクロボット「ファナック M-1iA」ミツイワ株式会社と株式会社オフィスエフエイ・コムです。
解決策と導入効果
パラレルリンクロボットの柔軟性とロボットビジョンの機能を最大限に活用し、機械的な規制ガイドや位置決め機構を排除することで、シンプルで多品種に対応できる自動化ラインを構築しました。これにより、製品ごとに発生するシステムインテグレーション費用や段取り替えの作業時間が大幅に低減されました。
また、各種画像検査装置を導入して品質保証力を強化し、各種システムとの連携により員数合わせや不良品集計などの業務を自動化することで、ライン管理者の負担も軽減されました。
結果として、労働生産性は4.1倍に向上し、作業人員は19名から7名に削減されました。生産現場からは好評を得ており、切り替え負担の低減は保全要員の負担軽減にもつながっています。投資回収年数は3.6年と見込まれています。
双腕型ロボットを活用した複数システム兼用可能な自動車部品の検査梱包工程の自動化
東洋ドライルーブ株式会社は、自動車部品の検査梱包工程に協働双腕ロボットを導入し自動化しました。このロボットは容易に移動可能で、複数のシステムで兼用することで導入コストを削減。少量多品種生産で費用回収が困難だった製品にもロボットシステム化を実現し、人とロボット、専用機が共存するシステムの構築を可能にしました。
導入前の課題
自動車部品のコーティング加工において、製品が少量多品種であるため、検査梱包工程の大部分が人の手や目に頼る作業となっていました。過去には専用設備に投資したものの、生産量減少で稼働率が低下する経験があり、費用回収が難しいことから、新たな設備投資に消極的でした。従来の産業用ロボット導入では安全柵が必要で、ロボットがアンカー固定されるため、部品ごとに専用システムを構築する必要があり、コストとスペースの課題がありました。
導入されたロボットとSIer
双腕型スカラロボット「川崎重工業 duAro」株式会社A-TECと株式会社明和機器です。
解決策と導入効果
協働双腕型ロボットを採用することで、ロボットが移動可能で安全柵が不要、かつ双腕型でコンパクトなシステムを実現しました。専用化する部分を最小限に抑え、複数のシステムでロボットを兼用できる仕組みを構築しました。これにより、人手に頼っていた作業のバラつきを抑え、品質の安定化を図ることが可能となりました。
この導入により、労働生産性は2.0倍に向上しました。作業人員は3名から2名に削減され、作業者の肉体的負担が軽減されました。複数のシステムでロボットを兼用できるという導入目標を達成し、今後のロボット導入に対する抵抗感が減少しました。投資回収年数は7.9年です。
外観検査自動化の方法
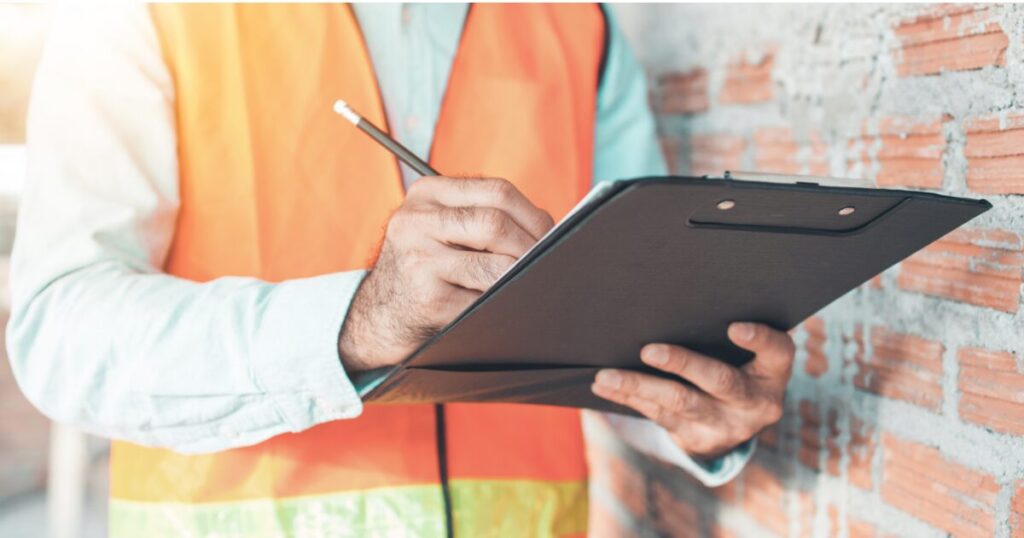
外観検査を自動化するには、ハードウェアとソフトウェアを組み合わせた専用のシステムを構築する必要があります。ここでは、一般的な自動化の流れと、その中で用いられる代表的な手法を紹介します。
自動化された外観検査の基本的なフローは次の通りです。
- ワークに照明を当て、安定した明るさで検査環境を整える
- 高精度カメラでワークを撮像する
- 撮像した画像データを画像処理ソフトで解析し、不良の有無を判定する
- 不良が検出された場合、対応処理を行う
それぞれ見ていきましょう。
不良品への対応方法
先ほど述べた一連の工程において、不良品の対応方法にはいくつかの選択肢があります。
人が不良品を確認・対応する
自動検出された不良品に対して、作業者が警報を受けて確認・仕分けを行う方式です。画像処理装置が異常を検出するとアラートが発信され、検査員がその内容をチェックして対処します。比較的低コストで始められる手法ですが、検査員の配置や対応スピードが生産効率に影響する可能性があります。
ロボットによる不良品の自動ハンドリング
画像処理で不良品が判定された際、ロボットアームが自動的にその製品を除去する方式です。ラインを止めずに不良品を取り除けるため、スループットを維持しつつ省人化を実現できます。ただし、ロボット動作に応じてラインスピードの調整が必要になる場合があります。
NGラインへの自動振り分け
不良が判明した製品を、自動的にNGラインへ搬送する方法です。制御装置がOK/NGの信号を出し、製品を適切なラインへと誘導します。完全自動で検査と分別を完結でき、特に大量生産において効果を発揮します。
AIを活用した画像認識による外観検査
近年ではAI技術を活用した画像解析システムの導入も進んでいます。AIは、大量の正常データや不良品の学習を通じて、判定精度を向上させることができます。
ルールベースの判定では対応が難しい微細な違いや、個体差のある製品の検査にも柔軟に対応できるのが強みです。特に多変量な不良形態を持つ製品の検査においては、AIが有効なソリューションとなります。
外観検査自動化に必要な装置構成
外観検査の自動化には、検査対象や目的に応じた構成機器の選定が不可欠です。主に以下のような機器が使われます。
- 照明機器:対象物の状態を明瞭に映すための光源(リングライト、バーライトなど)
- レンズ付きカメラ:表面の傷や異物を高精度に捉えるための撮像装置
- 画像処理ソフト/AIエンジン:撮像データを解析し、基準との違いを判定するソフトウェア
- 制御システム:NG品の搬出、アラート通知、ライン停止などを制御するPLCやPC
これらをワークに合わせて適切に組み合わせることで、効果的な外観検査の自動化が実現します。近年では、これら一式をパッケージ化したシステムも多くのSIerから提供されています。
失敗しない外観検査の自動化導入のやり方
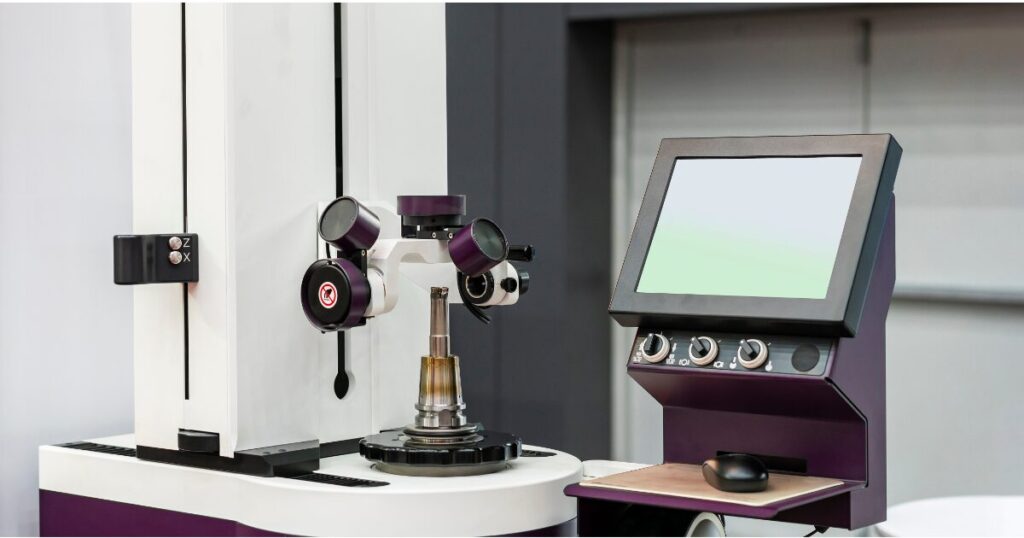
外観検査の自動化は、品質安定や人手不足対策に有効ですが、導入の進め方を誤ると期待した効果が得られないこともあります。ここでは、導入を成功に導くためのステップと注意点を具体的にご紹介します。
外観検査の課題を定義する
まず取り組むべきは、自社の外観検査における現状の課題を明確にすることです。課題の可視化なしに自動化の方向性を決めると、導入後のトラブルや想定外のコスト増につながります。
以下のような点を洗い出すことが有効です。
- 現在の検査スピードと必要な処理量にギャップがあるか
- 検査員の人数や技術レベルが品質要求に見合っているか
- 作業者ごとの判定基準にバラつきがないか
- 検査結果の記録やトレーサビリティが確保されているか
- 不良の傾向を分析できる体制があるか
こうした情報を整理することで、自動化が本当に必要なポイントや、改善すべき検査フローが見えてきます。
自動化の対象範囲を決める
すべての工程を一気に自動化するのではなく、効果が見込める領域から段階的に導入するのが現実的です。
例えば、欠陥の種類によっては人間の目での判断が有利なケースもあります。細かなキズや異常な反射光、ほこりのような微小要素の判別は、AIや画像処理だけでは難しい場合があります。
そのため
- 「微細な傷の検出」は目視
- 「形状不良の検出」は自動化
といったように、工程を分けて機械と人を役割分担させることが、コストと精度のバランスを取る上で重要です。
適切なシステム・レンズ・照明を選ぶ
自動化の対象が定まったら、それに合ったシステムや構成機器の選定が必要です。最近ではAIを搭載した外観検査装置も登場しており、対象物や要求される検査精度に応じた選定が求められます。
特に見落とされがちなのがレンズと照明の選び方です。画像処理の精度は、カメラやソフトウェアだけでなく、「いかにきれいに対象を撮像できるか」によっても大きく左右されます。
レンズ選びのポイント
レンズ選定では主に以下の2点が重要です。
- 焦点距離:撮影距離に応じて適切な焦点距離(例:8mm/16mm/25mm)を選び、対象をしっかりフレーミングできるかがポイントです。
- 被写界深度:製品表面に凹凸がある場合、ピントの合う範囲が広いレンズを選ぶことで、ぼやけの少ない画像が得られます。
例えば高低差のある製品では、マクロレンズではなく、やや距離を取った位置からの撮影と強力な照明の組み合わせが効果的です。
照明選びのポイント
照明は検査画像の明瞭さを大きく左右します。
照射方法や光の拡散性を製品に合わせて選定しましょう。
検査対象 | 推奨照明タイプ |
---|---|
金属表面の刻印検査 | 正反射LED照明 |
フィルム越しの印字確認 | 拡散反射LED照明 |
端子の寸法測定 | 透過型LED照明 |
それぞれの照明には得意な反射・透過の特性があり、形状や材質に応じた選択が重要です。均一で明るい照射環境が整っていないと、画像処理の精度が著しく低下します。
導入後も継続的な管理・メンテナンスを行う
外観検査の自動化は、導入したら終わりではありません。システムの状態を定期的に確認し、カメラ・照明・検査ソフトのパラメータを見直していく必要があります。
また、AI搭載システムでは検査対象の変化に応じた再学習も必要です。初期に設定した条件のまま運用を続けると、経年劣化やライン変更によって誤判定が増えるリスクもあります。
- 機器の清掃やキャリブレーションの定期実施
- 検査データの蓄積と再学習
- 新製品・新素材への対応調整
こうした継続的なメンテナンス体制を構築することが、検査精度の維持とライン安定化につながります。
外観検査の自動化を実現するおすすめ関連製品

外観検査を自動化するためには、検査対象や目的に応じた機器・ソフトウェアの選定が不可欠です。ここでは、導入の検討に役立つ注目の製品・ソリューションを紹介します。
製品名 | 詳細 |
---|---|
TECHVIEW 画像処理開発ツール | 製造現場のスタッフでも扱いやすいUI設計で、専門知識がなくても簡単に画像検査アプリの開発・調整が可能 |
Deama(ディアマ)画像検査システム | AIとOCRを融合した検査システムで、印字や色味、異物混入などのチェックを高速かつ高精度に実行できる |
iRAYPLE カメラシリーズ | 豊富なラインナップを持つ産業用カメラブランドで、さまざまな検査ニーズに対応可能な高性能マシンビジョン機器を提供している |
URCP 検査ソリューション | カスタマイズ性が高く、ソフトとハードを一体で提案・導入。ニーズに応じた柔軟な対応が可能な画像処理ソリューション |
EYEbeGenesis+(アイビージェネシスプラス) | 少量データでの学習に対応する第3世代AIを搭載。ヒトの視覚に近い判断で微細な欠陥も見逃さず検出する |
ラインスキャンカメラ各種 | 高速で流れる製品のライン検査に特化したカメラ。連続画像の取得によって、広範囲の高精度検査を実現する |
ZENAI(ゼナイ)AI検査システム | ディープラーニングにより、複雑な表面欠陥の判定を自動化。高速処理(0.1秒判定)で生産ラインにも対応可能 |
フォトナビ・目視レス | 独自の画像認識アルゴリズム「ABHB」を活用。不定形な対象でも検出可能で、トータル提案にも対応した製品 |
エンベッデッドビジョンカメラ | 小型筐体に画像処理機能を内蔵。世界最小クラスのスマートカメラで、組込型の外観検査にも適している |
DeepSky(ディープスカイ) | 画像収集からAI学習・判定までを1台で実現。現場目線で設計されており、導入・設定もシンプル |
TESRAY Sシリーズ | ロボットと撮像モジュール、AIを組み合わせた高精度な外観検査システム。形状の複雑なワークにも対応できる |
RoxyAI | 製造現場の実情に即したAI画像検査ソリューション。自動化全体の構築支援にも強みがある |
メイコー 自動検査システム | 搬送から欠陥判定・除去まで一貫して自動化。学習機能付きで検査範囲の変化にも柔軟に対応可能 |
GK-2000 外観検査装置 | 高解像度・高速処理に対応したラインセンサ。不良検知時には信号出力・画像保存も行える拡張性の高いモデル |
外観検査の自動化ならBRICSにご相談ください
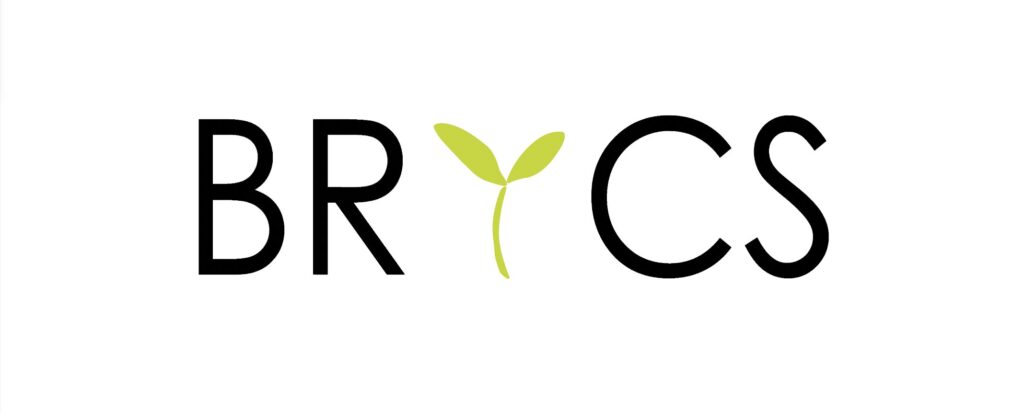
外観検査を自動化したい・目視検査を機械に置き換えたい方は、ぜひロボットシステムインテグレータのBRICSにご相談ください。
BRICSでは累計200社以上の工場自動化の支援をおこなってきました。ハードウェアエンジニアとソフトウェアエンジニアの両方が在籍しているため、お客様の現状の課題に合わせた、自動化支援が可能です。
無料相談を受け付けておりますので、ぜひお気軽にお問い合わせください。
\ 話を聞いてみたいだけでもOK /
外観検査の自動化におけるよくある質問
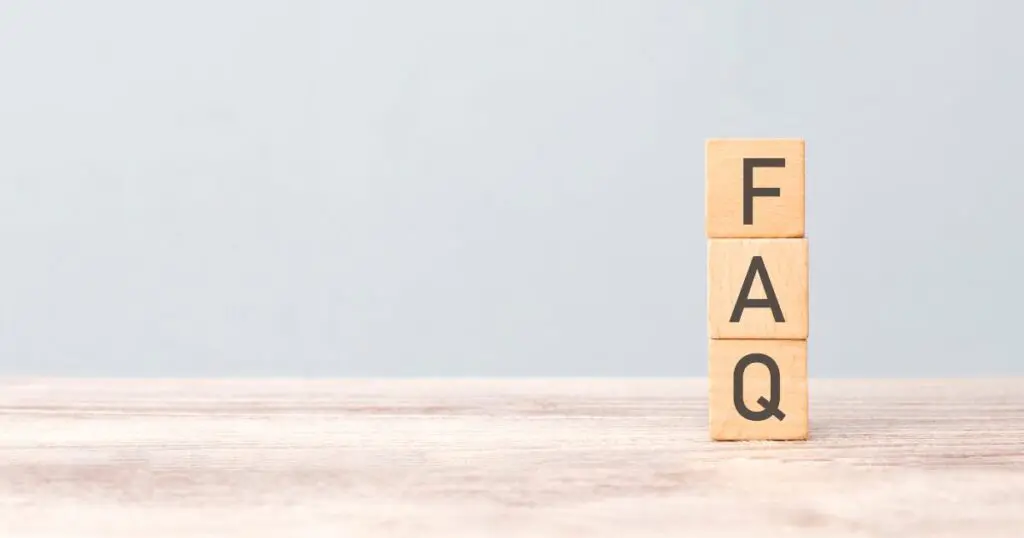
ここからは外観検査の自動化に興味のある方がよく抱く疑問にお答えします。
AIによる外観検査のデメリットは?
AIを活用した外観検査は、高精度な判定や微細な欠陥の検出に優れていますが、導入や運用においてはいくつかの注意点もあります。
主なデメリットは以下の通りです。
初期導入の手間とコストがかかる
AIシステムを構築するには、カメラや照明、処理用PCなどの設備に加え、AIモデルの学習用画像を大量に準備する必要があります。導入費用だけでなく、現場環境に合わせたチューニングにも時間がかかる場合があります。
データが不十分だと誤判定が増える
学習用画像が不足していたり、ばらつきのあるデータで学習した場合、実運用時に想定外の誤判定が発生することもあります。導入後も継続的なデータ追加と再学習が重要です。
すべての検査に適しているわけではない
例えば、光の反射で見え方が変わる傷や、検査対象の個体差が大きすぎる場合など、AIだけでは判定が難しいケースもあります。こうした場合には、目視との併用やルールベース処理との組み合わせが有効です。
AI外観検査は非常に強力なツールですが、過信せず、導入前に自社の製品特性と運用体制に合っているかをしっかり見極めることが大切です。
自動外観検査装置とは何ですか?
自動外観検査装置とは、製品の表面にあるキズや汚れ、異物混入、ひび割れなどの欠陥を、人の目ではなくカメラと画像処理技術で検出・判定するための装置です。省人化と品質安定を両立する手段として、多くの製造現場で導入が進んでいます。
活用事例としては以下のようなものが挙げられます。
- 半導体や電子部品のパターン検査
- 医薬品の錠剤やラベルのチェック
- 食品パッケージや内容物の異物検出
- 金属・樹脂部品のバリや欠けの検査
自動外観検査装置は「人に代わって品質検査を行う目」として、品質管理の標準化や検査工数の削減に貢献しています。特に、安定した生産と品質向上を両立したい現場にとって、導入価値の高い装置と言えるでしょう。
まとめ
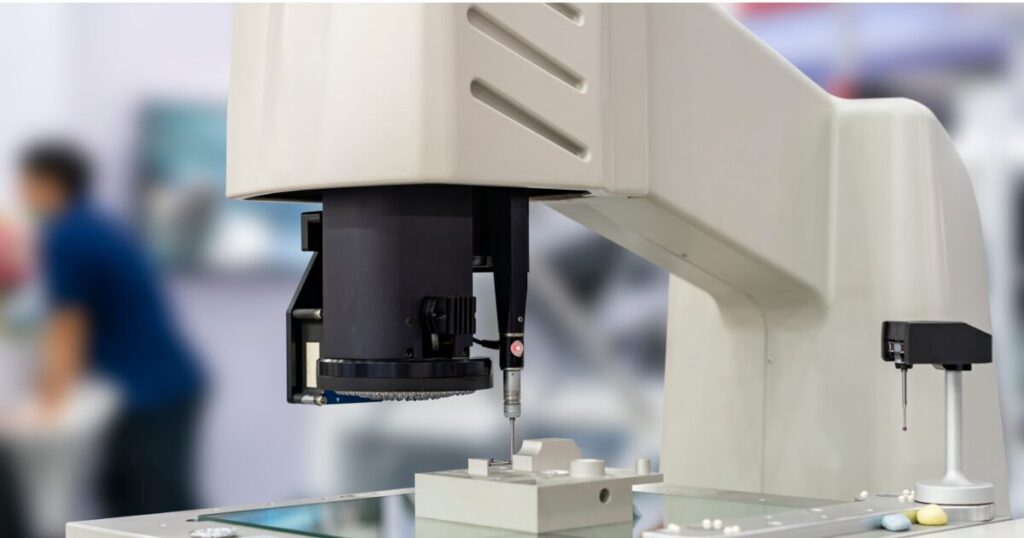
本記事では、外観検査の自動化について、その基本概念やメリット、導入時の課題、成功事例、そしておすすめ製品までを幅広く解説しました。検査精度の向上やコスト削減、人手不足への対応といった利点がある一方で、装置のカスタマイズや人材確保など、現場に応じた工夫も必要です。
まずは自社の課題を明確にし、適切な範囲から段階的に導入を進めることが外観検査を自動化させる上で重要です。導入を検討中の方は、ぜひBRICSへご相談ください。
\ 話を聞いてみたいだけでもOK /