工場の省人化に取り組みたい・製造ラインにロボットやシステムを導入したいとお考えですか。
本記事では、工場省人化の定義やメリット・取り組む際の課題を紹介します。さらに省人化における注意点や失敗しない進め方も紹介します。
ファクトリーオートメーション化のプロが徹底解説するので、工場における生産・製造ラインを省人化したいという方は、ぜひ最後までご覧ください。
工場の省人化(しょうじんか)とは
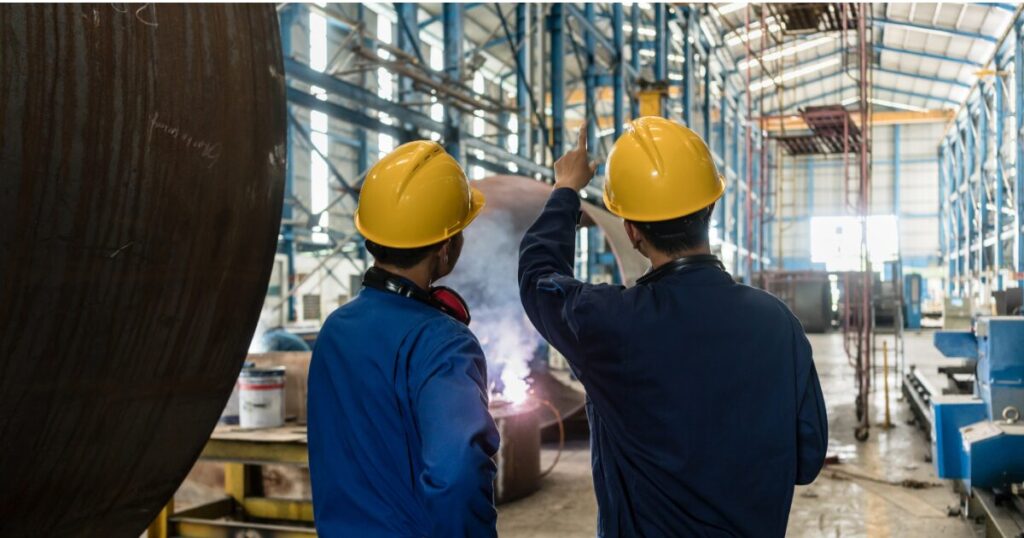
省人化とは、これまで複数の作業員が担当していた工程を、設備やシステムの導入によって少人数でまかなえるようにする取り組みです。単なる作業の効率化にとどまらず、「人の数を減らす」こと自体が目的であり、製造業においては古くから注目されてきました。
とくに昨今では、人手不足や高齢化が進行する中で、現場の生産性と持続性を両立させるための解決策として、省人化が再び注目を集めています。産業用ロボットや協働ロボット、自動搬送装置(AGV)、AI搭載の検査装置など、先端技術の活用により、省人化の実現がより現実的になってきました。
また、単に機械化するだけではなく、作業工程の見直しや業務の標準化も重要です。現場のムダをなくし、属人化を防ぐことで、少人数でも安定した品質・生産スピードを維持できる体制づくりが進められています。
「工場の省人化」と「工場の省力化」との違い
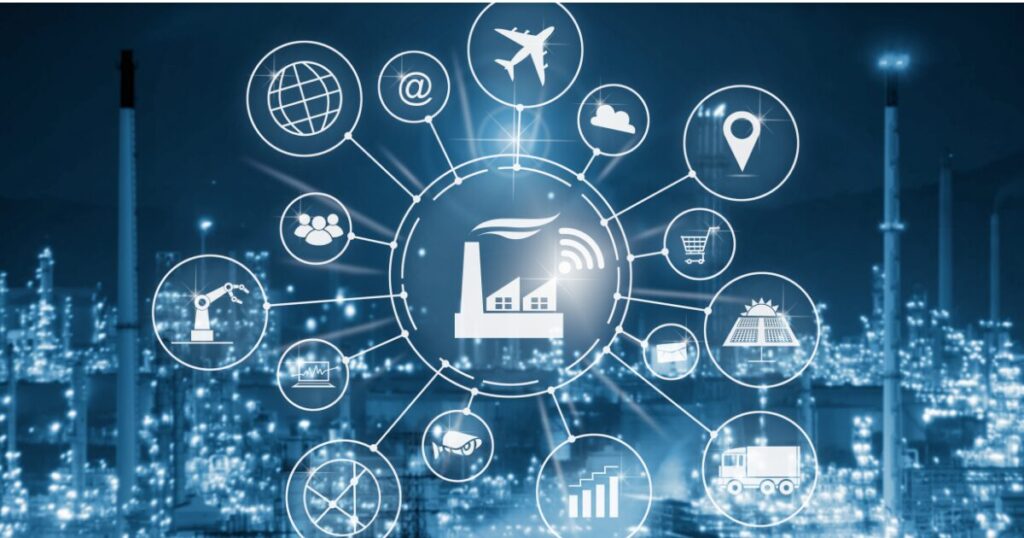
工場の業務改善においてよく使われる言葉に「省人化」と「省力化」があります。どちらも効率化を目的とした取り組みですが、その意味や最終的な目的には明確な違いがあります。
工場の省人化は「人の数を減らす」ことが主眼です。
例えば、5人で行っていた検査工程を自動検査装置の導入により3人に削減できた場合、省人化に成功したと言えます。省人化が進めば、その分の人件費削減や、他部署への人員の再配置といったコストメリットが生まれます。
工場の省力化は作業そのものの負担や手間を減らすことを目的とした改善活動です。
例えば、重い部品を運ぶ工程に補助装置を導入して作業者の身体的負担を軽減したり、作業手順を簡素化することで業務のスピードを高めたりする施策が該当します。こうした取り組みは、作業者の安全性や快適性を高める効果がある一方で、人員の数を減らすことを直接の目的としているわけではありません。
つまり、省力化は作業を「楽にする」手段、省人化は作業を「減らす」仕組みであると整理できます。省力化を積み重ねた先に、省人化が実現するケースも多く、両者は段階的に活用されることが理想です。
工場の省人化と少人化との違い
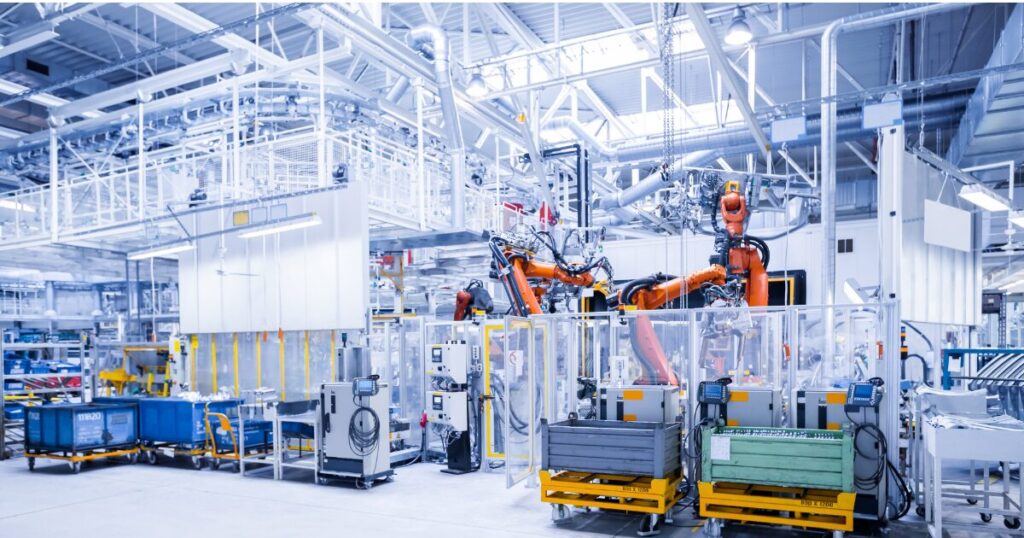
省人化に似た概念として「少人化」があります。これは、省人化の延長線上にある考え方であり、現場の柔軟性が問われる高度な仕組みです。
少人化は、製品の生産量に応じて最適な人数を柔軟に配置し、常に最少人数で業務を遂行する体制を指します。例えば、繁忙期は10人で対応し、閑散期には5人で運用するなど、生産数に応じて人員を調整することを前提としています。
この考え方は、特に受注量が不安定な業界や、カスタマイズ生産が多い現場で有効です。常にフル稼働の体制を維持するのではなく、必要なときに必要なだけの人材を配置することで、ムダな人件費を抑えながらも品質を確保できます。
一方で、省人化はあくまで常時人員を減らすことを目指すものであり、柔軟性よりも「固定的な削減」に重点を置いた取り組みです。
工場に省人化が求められる・必要な理由
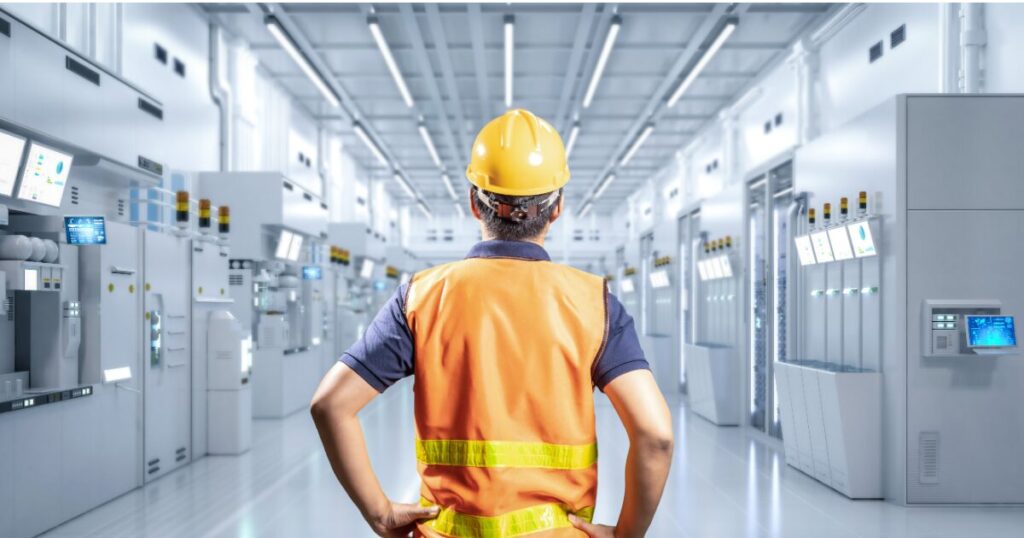
日本の製造業が直面している課題のひとつに「省人化」があります。これは単なる人件費削減の施策ではなく、企業の将来性や競争力を維持・強化するために重要です。
ここでは、工場において省人化が求められる主な理由を詳しく解説します。
- 人手不足を解消するため
- 人件費抑制や製品コストダウンに繋がるため
- 生産性を向上するため
- 製造現場の環境を改善するため
- 技術・技能承継問題を解消するため
それぞれ見ていきましょう。
人手不足を解消するため
製造業では慢性的な人手不足が深刻化しています。とくに若年層の製造業離れや、熟練工の高齢化による退職の波は、現場の稼働そのものを脅かすレベルに達しつつあります。 生産年齢人口の減少という社会的背景に加え、体力的負担の大きさや、3K(きつい・汚い・危険)というマイナスイメージも相まって、新たな人材の確保がますます難しくなっているのが現状です。
こうした状況の中、省人化は「限られた人数で安定した生産活動を維持するための根本的な対策」として位置づけられています。ロボットや自動化装置を活用することで、人手に頼らない持続的な生産体制の構築が可能になります。
人件費抑制や製品コストダウンに繋がるため
製品価格の競争が激化する中、人件費は製造原価の中でも大きなウエイトを占める固定費です。とくに中小企業では、人件費の高騰が経営を圧迫するケースも珍しくありません。 業務の自動化や省人化によって、同じ生産量をより少ない人数で実現できれば、直接的なコストダウンに繋がります。
また、人件費が削減されることで、浮いた資金を設備投資や製品開発、人材育成などの成長領域へ再分配することも可能です。 単なる節約ではなく、「コスト構造の転換」を目的とした省人化は、企業の競争力を中長期的に底上げする有効な手段と言えるでしょう。
生産性を向上するため
生産性の向上は、売上増加とコスト削減の両方を実現する最も効果的なアプローチです。省人化によって導入される自動化機器やシステムは、作業のムラや無駄を排除し、一定のスピードと品質で生産できるため、人的リソースに依存しない生産体制を構築できます。
さらに、IoTやAIといった技術と連携させることで、機器の稼働状況や不良品の発生状況などのデータをリアルタイムで把握でき、改善サイクルをより精緻に回すことも可能になります。 これにより、現場レベルだけでなく全社的な生産戦略の高度化にもつながります。
製造現場の作業環境を改善するため
工場の省人化は、単に人員数を減らすだけではありません。危険な作業、身体的に過酷な作業、単調な反復作業など、従業員にとって負担の大きい業務を自動化することで、職場環境そのものを改善するという側面もあります。 これにより、作業者の安全性が高まり、労災リスクの低減にもつながります。
また、労働時間の短縮や休暇の取得促進にも貢献するため、従業員満足度の向上や離職率の低下といった効果も期待できます。 省人化は「人を減らす」ことだけでなく、「働きやすさを高める」ための手段でもあるのです。
技術・技能承継問題を解消するため
製造現場では、熟練作業員の技術やノウハウに依存していた工程が多く、いわゆる「職人技」の継承が課題となっています。しかし、個人の経験や勘に頼った技術は、標準化が難しく、退職と同時にその技術が失われてしまうというリスクを抱えています。
省人化のプロセスでは、こうした技術の可視化・マニュアル化・自動化を進めることで、属人的な要素を減らし、安定した生産品質を保つことが可能になります。 また、技能の一部を自動機に置き換えることで、若手や未経験者でも短期間で現場戦力となれる仕組みが構築でき、結果として「技術の断絶リスク」も低減できます。
工場の省人化のメリット
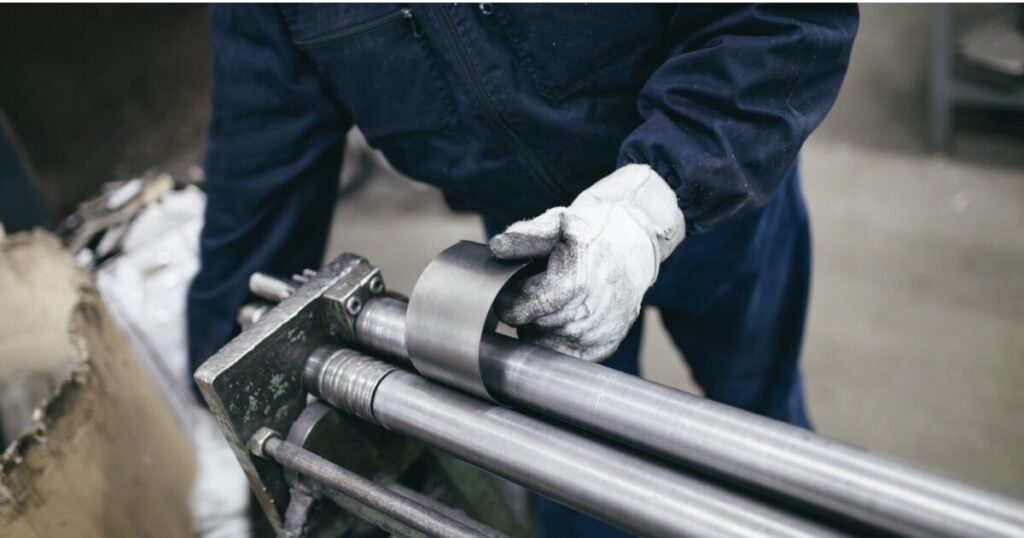
工場の省人化は、単なる人員削減・人件費削減ではなく、工場全体の生産性を高める戦略的な施策です。ここでは、省人化に取り組むことで得られる代表的なメリットを簡潔に紹介します。
メリット | 詳細 |
---|---|
限られた人材を有効活用できる | 定型業務を自動化することで、人は判断・調整・改善などの付加価値の高い業務に集中でき、全体の生産性が向上する |
品質のばらつきが抑えられる | 自動化によって作業の均質化が進み、作業者の熟練度に左右されない安定した品質を実現できる |
データに基づいた改善が可能になる | IoTやセンサーを備えた省人化装置の導入により、作業状況や生産データの可視化が進み、改善サイクルがよりスピーディーになる |
教育・技能継承の効率化 | 属人的だった技術を仕組み化・マニュアル化することで、新人育成のスピードが上がり、教育コストの削減にもつながる |
働きやすい職場環境の実現 | 負荷の大きい作業を自動化することで、労働環境が改善され、離職率の低下や採用活動の成果向上にも貢献する |
工場の省人化のデメリットや注意点
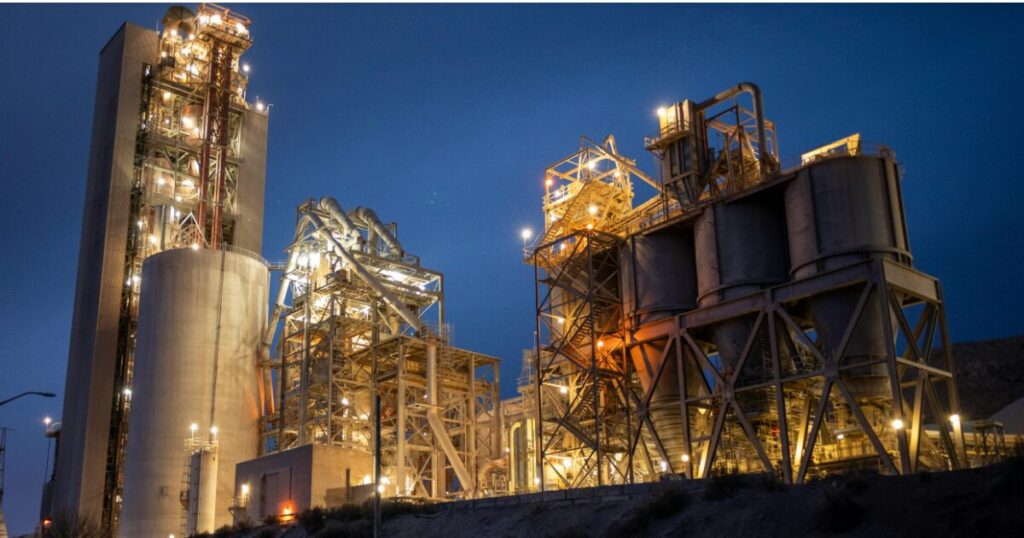
工場の省人化は多くのメリットをもたらしますが、導入や運用にあたっては慎重な検討が必要です。特に導入初期には課題や負担が発生しやすく、適切な対策を講じなければ逆効果となる可能性もあります。ここでは、省人化に取り組む際に押さえておきたい代表的なデメリットや注意点を紹介します。
- 導入やメンテナンスにコストがかかる
- ロボットやシステムに精通した人材が必要である
- 作業スペースの確保が必要になる
それぞれ見ていきましょう。
導入やメンテナンスにコストがかかる
省人化を進めるには、多くの場合で自動化装置やロボット、制御システムの導入が必要となり、それに伴って初期投資が発生します。導入する機器の種類や規模にもよりますが、数百万円~数千万円規模の費用がかかることも少なくありません。
また、導入後のメンテナンス費用も継続的に発生します。消耗部品の交換、ソフトウェアの更新、トラブル時の復旧対応など、稼働を維持するための保守体制にもコストがかかる点を念頭に置いておく必要があります。
さらに、新しい設備を導入する際には、従業員への操作教育やマニュアル整備も必要です。教育期間中は一時的に生産効率が落ちる可能性があるため、スケジュールや体制面でも余裕を持った導入計画が求められます。
ロボットやシステムに精通した人材が必要である
いくら優れた装置を導入しても、それを正しく使いこなせなければ省人化の効果は限定的です。とくに近年では、ロボット制御、PLC、IoT、AIといった高度な知識が求められるシステムが増えており、操作・保守・トラブル対応のためには専門的なスキルを持った人材が不可欠です。
しかし、こうした人材は市場でも希少性が高く、自社で採用するには高コストがかかる可能性があります。社内で育成する場合も、指導できる技術者が必要なうえ、教育担当者の負担や工数の増加にも注意が必要です。
さらに、現場と管理部門の間で「技術が理解されていない」「実態に合わない機器が導入された」などのミスマッチが起きると、従業員の不満や運用トラブルにつながるリスクもあるため、導入前の丁寧なヒアリングと説明が欠かせません。
作業スペースの確保が必要になる
自動化装置やロボットを導入する際には、それらを設置するための十分なスペースが必要です。限られた面積の工場では、新しい機器の導入が人の動線や既存作業の安全性に影響を及ぼすこともあります。
例えば、ロボットアームの可動範囲や安全柵の設置が必要な場合、従来の作業場所が狭くなり、かえって作業性が落ちてしまうこともあるでしょう。また、安全面を考慮して、装置と人の距離を一定以上確保しなければならないケースもあります。 導入前には、機器の設置スペースだけでなく、人の作業環境や避難経路、安全確保などを含めたレイアウト全体を見直し、現場と連携したうえでの計画策定が求められます。
工場、生産ラインの省人化を実現する具体的な方法
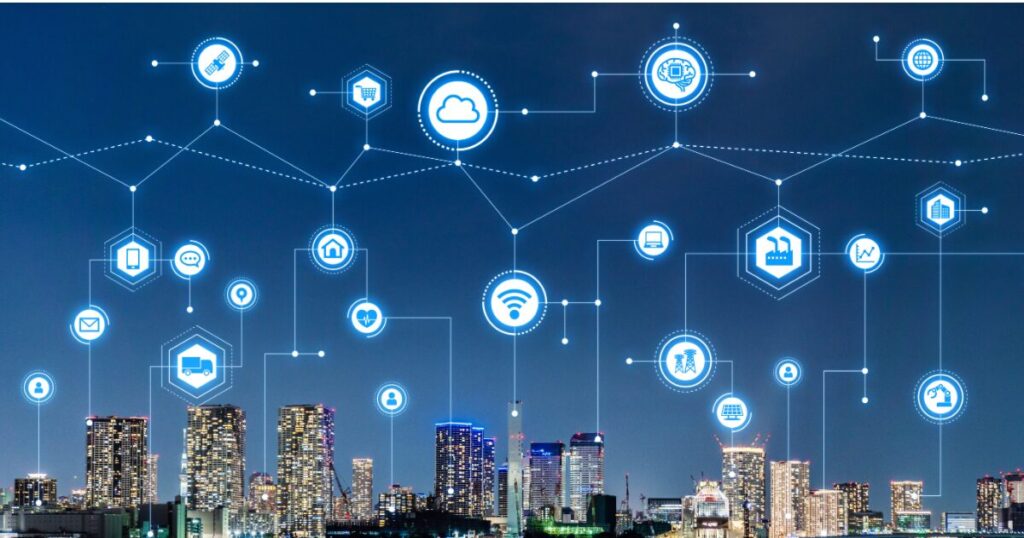
省人化の実現には、「人にしかできない業務」と「機械に任せられる業務」を見極め、それぞれに最適な手段を講じることが重要です。ここでは、現場で取り組みやすい具体的な施策を紹介します。
- AIやIoT、ロボットを活用した自動化
- 作業プロセスの見直し、業務効率を改善
それぞれ見ていきましょう。
AIやIoT、ロボットを活用した自動化
近年、多くの工場で導入が進んでいるのが、AI・IoT・ロボットといった先端技術を活用した自動化です。これらは、人的リソースを削減しながらも生産性や品質を維持・向上させる鍵となります。
例えば、画像認識AIを活用して製品の外観検査を自動化すれば、人の目によるばらつきを防ぎ、検査時間も短縮できます。また、センサーとIoTを連携させることで、設備の状態監視や稼働データの収集が可能になり、不具合の予兆検知やメンテナンス時期の最適化(予知保全)にもつながります。
産業用ロボットを導入するケースも一般的で、組み立てや搬送、溶接、ピッキングなどの定型作業を自動化することで、従来4~5人が必要だった工程を2~3人に削減した事例も多数あります。
これらの技術を総合的に活用するスマートファクトリーの構築は、今後の製造業における省人化の理想的な形といえるでしょう。
AIやIoT、ロボットを活用した自動化についてはこちらの記事でも解説しています。
工場の自動化とは?メリット・課題・成功事例・進め方を徹底解説
作業プロセスの見直し、業務効率を改善
テクノロジーの導入以前に、まず行いたいのが「現場の作業内容そのものの見直し」です。長年の慣習や暗黙のルールで続けられている作業の中には、すでに不要となっている工程や、他の工程と統合できる作業も少なくありません。
例えば、紙ベースの記録作業をタブレット入力に切り替えるだけでも、転記作業やヒューマンエラーを削減でき、省人化の第一歩になります。また、工程ごとの作業時間や負荷を洗い出すことで、改善の余地がある部分を可視化でき、ボトルネックの解消にもつながります。
このような業務フローの最適化は、特別な設備投資を必要とせず、比較的低コストで取り組める点が魅力です。定期的な現場ヒアリングや作業分析を通じて、小さな改善を積み重ねることが、最終的には大きな省人化効果を生み出す土台となります。
失敗しない!工場の省人化の進め方
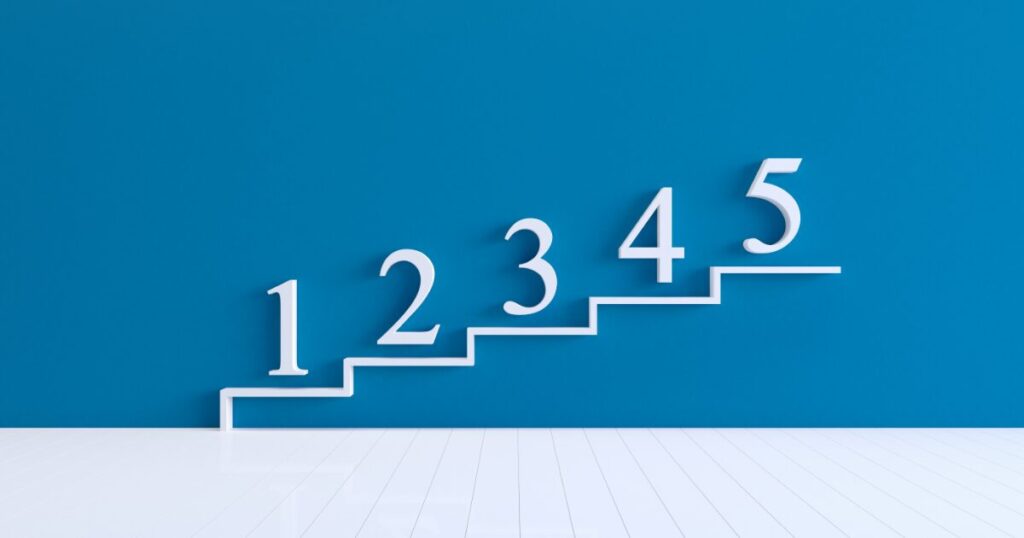
省人化の導入には明確な手順と戦略が必要です。やみくもに設備を導入しても、期待通りの成果が出ないどころか、現場の混乱を招くこともあります。ここでは、効果的かつ失敗しにくい省人化の進め方をステップに分けてご紹介します。
- 既存業務の分析と見直しをする
- 作業の標準化・文書化をする
- 生産・製造ラインにロボットなどの設備導入し、自動化・効率化する
それぞれ1つずつ見ていきましょう。
既存業務の分析と見直しをする
省人化の第一歩は、現状の業務や工程を「見える化」することです。 まずは、すべての作業を洗い出し、それぞれの工程にかかる時間・負荷・必要人員などを数値で把握することから始めましょう。
作業内容の棚卸を行うと、思いのほか「やらなくてもいい作業」「本来の目的に貢献していない工程」が見つかることも多くあります。
また、熟練者に依存していた業務や、手戻りが多い工程などは、改善や自動化の対象として有力です。
この段階で大切なのは、「省人化=人を減らすこと」と短絡的に考えず、全体最適の視点で無駄を取り除き、限られた人材を戦略的に活用するための基盤づくりだと認識することです。
作業の標準化・文書化をする
工程分析の次は、作業手順を標準化し、文書化(マニュアル化)するフェーズです。 属人的な作業が多い現場では、省人化や自動化を導入しても成果が出にくく、作業のばらつきによる品質不良やトラブルの温床になりがちです。
標準化とは、誰がやっても同じ手順・同じ結果が出せるように作業を整えること。
そして、それをマニュアルや動画、手順書といった形で「誰にでもわかるように伝える」ことが文書化です。
この過程によって、作業の可視化・再現性の確保・教育の効率化が可能となり、将来的な自動化との連携もしやすくなります。
例えば、AI検査装置を導入する場合も、判定基準が人ごとに違えばトラブルが生じます。標準化された判断基準があるからこそ、AIにも正確な条件設定ができるのです。
生産・製造ラインにロボットなどの設備導入し、自動化・効率化する
分析・標準化が整ったら、いよいよ自動化・省人化に向けた設備導入の段階です。 とはいえ、すべてを一度に自動化する必要はありません。まずは「人手がかかりすぎている工程」「ヒューマンエラーが起きやすい工程」など、効果が見込める部分から段階的に導入していくのが現実的です。
近年では、産業用ロボットやAGV(無人搬送車)、AIを活用した画像検査装置などの導入が進んでおり、作業者1人あたりの負担を大幅に軽減することが可能になっています。
また、IoT技術と連携させれば、設備の稼働状況やトラブル傾向のデータをリアルタイムで可視化でき、さらなる業務改善にも活用できます。
ただし、設備導入にはコストと運用体制の整備も必要です。どの工程を自動化すれば最も費用対効果が高いかを見極めたうえで、必要な人材の育成・教育もセットで計画しておくことが成功のカギになります。
生産ライン・工場の省人化の導入成功事例
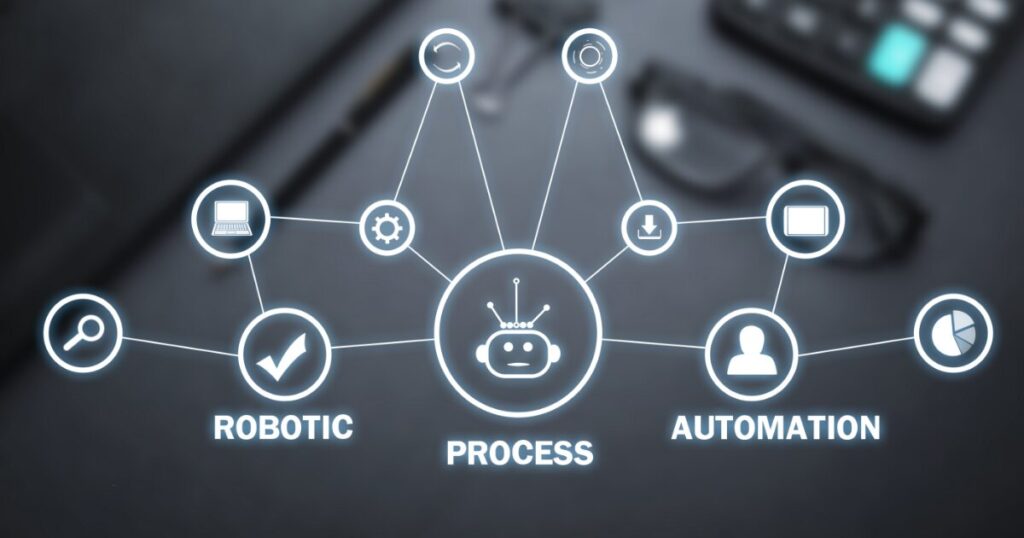
経済産業省のロボット導入実証事例を参照すると、熊本県のナカガワフーズでは、真空冷凍パック製品の箱詰め〜パレット積み工程にロボットを導入し、省人化を実現しました。
以前は30名体制で対応していた中、重労働となっていた工程をロボット化することで、8名から2名へと6名の削減に成功。削減された人員は他工程へ再配置され、生産性が4.4倍に向上しました。多品種対応のため、ロボット制御や段ボール供給との連携も最適化され、投資回収は約1.4年と見込まれています。
以下はBRICSが省人化に貢献した鋳造品製造ラインです。従来の14名体制から完全な無人化を実現。人材確保の問題を解消するとともに、安定した品質と高い生産効率を両立した柔軟なライン運営が可能となりました。スマートファクトリーのわかりやすい成功事例です。
工場の省人化・自動化業者をお探しならBRICSにお任せください
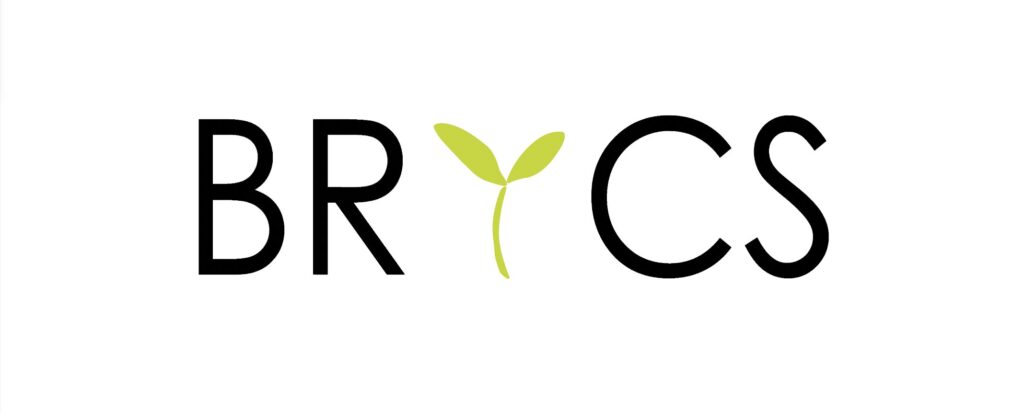
工場を省人化したい・自動化したいとお悩みの方は、ぜひロボットシステムインテグレータのBRICSにお任せください。
株式会社BRICSでは累計200社以上の工場自動化の支援をおこなってきました。ハードウェアエンジニアとソフトウェアエンジニアの両方が在籍しているため、お客様の現状の課題に合わせた、自動化支援が可能です。
無料相談を受け付けておりますので、ぜひお気軽にお問い合わせください。
\ 話を聞いてみたいだけでもOK /
製造業・工場の省人化におけるよくある質問
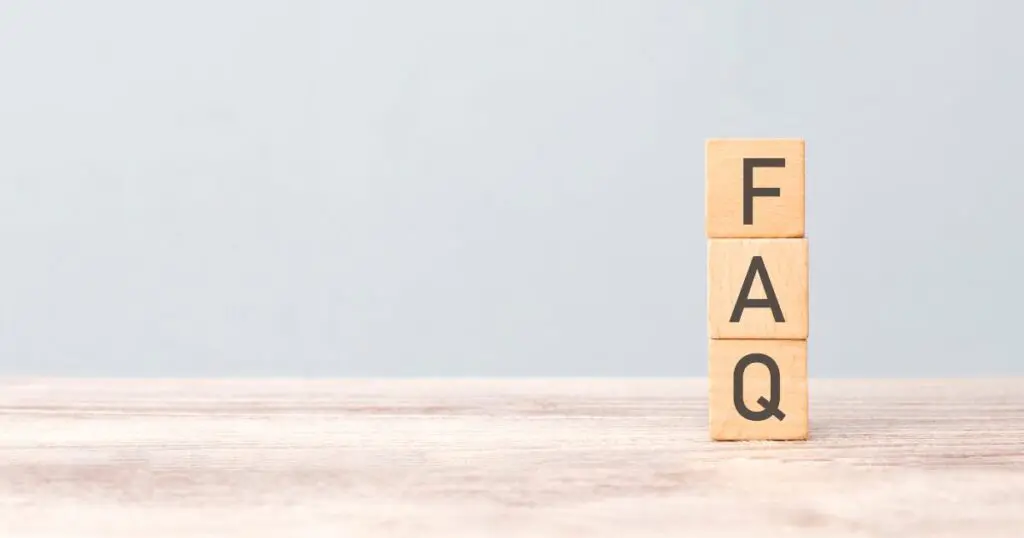
ここからは工場の省人化に興味のある方がよく抱く疑問にお答えします。
省人化の言い換えは?
「省人化」という言葉は、状況に応じてさまざまな言い換えが使われています。代表的なものとしては以下のような用語があります。
言い換え | 詳細 |
---|---|
省力化 | 人の数ではなく「作業の負担」を軽くすることに重点を置いた取り組み 作業者の身体的負荷を軽減したり、効率の良い手順に変えたりすることで、快適で安全な作業環境を実現する 必ずしも人員削減につながるとは限らない |
少人化 | 生産量や作業量の変動に応じて、常に最適最小限の人員で運用する体制を指す 繁忙期・閑散期に合わせて柔軟に人を配置できるようにする考え方 |
自動化・業務効率化・人員最適化 | いずれも省人化の文脈で使われることがある表現ですが、それぞれ意味や目的は異なる 自動化=作業の自動化、業務効率化=工程全体の最適化、人員最適化=人の配置を最適にする施策を意味する |
工場の自動化と省人化の違いは?
省人化と自動化は混同されやすい言葉ですが、「目的」と「手段」の違いに注目すると理解しやすくなります。
項目 | 自動化 | 省人化 |
---|---|---|
定義 | 機械やIT技術で作業を自動化すること | 必要な人員数を減らす取り組み |
目的 | 作業の効率化・品質向上・24時間稼働 | 人件費削減・人手不足の解消・生産性向上 |
方法 | ロボット、AI、IoT、システムの導入 | 業務改善+自動化+配置見直し |
主な効果 | 作業精度向上、ヒューマンエラー減少 | 人件費削減、人的リソースの再配置 |
つまり、自動化は省人化の一手段であり、すべての省人化が自動化を伴うわけではありません。業務フローの見直しや工程統合なども省人化の一部です。
工場の省人化進行における課題は?
省人化を推進する際、企業はさまざまな壁に直面します。代表的な課題としては、以下のようなものがあります。
省人化進行における課題 | 詳細 |
---|---|
初期投資とランニングコストの負担 | ロボットやAI、IoTシステムの導入には高額な初期費用が発生します。導入後も定期的なメンテナンスや保守契約が必要となり、費用対効果の見極めが重要です。 |
人材の教育・技術習得 | 最新技術を導入しても、使いこなせる人材がいなければ真価は発揮されません。現場オペレーターや保守担当者への継続的な教育体制が求められます。 |
柔軟性の低下 | 自動化されたシステムは、変種変量・短納期といった変化には対応しにくい面があります。特に少量多品種生産や急なオーダー変更には柔軟性を確保する工夫が必要です。 |
既存設備との連携の難しさ | 既存の機械やシステムと新しい自動化設備がうまく連動しないことで、生産効率がかえって落ちるケースもあります。事前のシステム設計やインフラの見直しが欠かせません。 |
技能継承とデジタル人材の不足 | 熟練工の退職により、技術の継承が進まない現場も多くあります。加えて、DXやITに対応できる人材の確保・育成が追いついていない中小企業も多く、組織的な人材戦略が求められています。 |
これらの課題を克服するには、技術導入と同時に「教育・組織づくり・現場との対話」をセットで進めることが重要です。単に設備を入れるだけでは省人化は成功しません。
まとめ
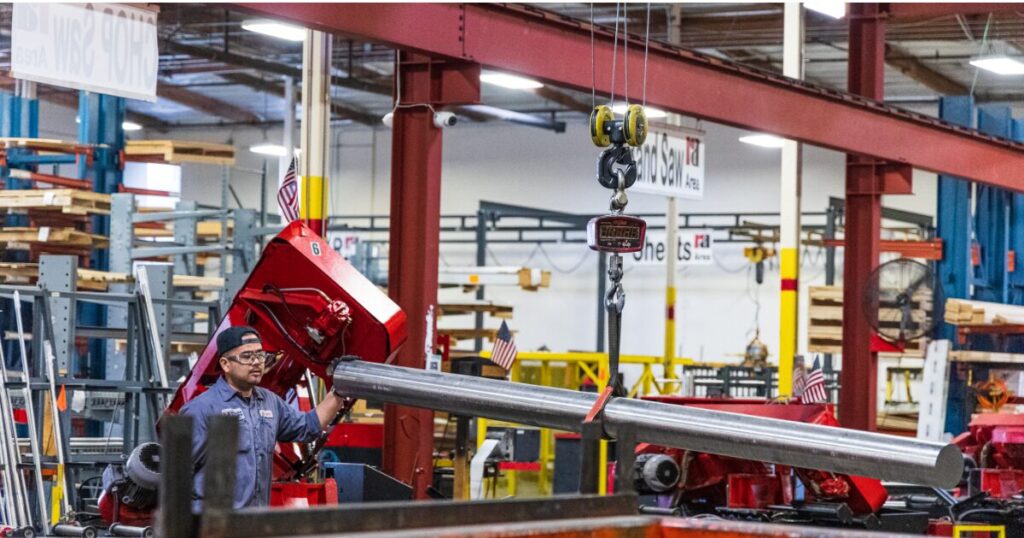
本記事では、工場の省人化について、その定義・省力化や少人化との違い・必要性・導入メリット・課題・具体策まで網羅的に解説しました。省人化は単なる人員削減ではなく、持続可能な生産体制の構築や人手不足対策、コスト削減、生産性向上など、製造現場の抜本的な課題解決に直結する重要な施策です。
ただし導入には初期投資や技術人材の確保など課題も伴います。まずは現場分析から始め、段階的に進めることが成功の鍵です。導入検討中の方はぜひBRICSへご相談ください。
\ 話を聞いてみたいだけでもOK /